Features
- Machine made entirely of AISI 304 stainless steel
- Lamination belt width from 240 to 400 mm
- Customizable line layout based on the product features
- Tunnel for cooling/holding the product before cutting the bars
- Bar cooling tunnel after cutting to optimize subsequent processes or packaging.
- Line speed and all cycle parameter settings via the HMI panel
- Possibility of remote control and monitoring for Industry 4.0 standard
Technical specifications
- Temperatures can be set in different areas ranging from -10°C/+100°C
- Bar width change via the HMI panel
- Product thickness adjustment from 5 to 25 mm
- Longitudinal cutting unit with multiple circular blade cutter
- Guillotine transverse cutting unit with pneumatic movement or ULTRASONIC cutting with mechanical movement driven by gearmotors.
- Bar separation system for end of line automation
- Lubrication system with release oil for extra sticky products.
We produce different types of automated lines for the production of cereal, energy, protein, high protein and fruit bars, as well as brittle and pastilles with a production capacity of 3,500 to 12,000 bars/h.
Our thirty years of experience, precision component design and the manufacturing quality of our systems ensure long-lasting durability coupled with excellent production rates over consecutive work shifts with minimum maintenance requirements.
All our automated systems can be tailored to the product and customer’s requirements and consist of the following:
- Temperature-controlled product loading area to maintain the mixture at the correct temperature.
- Laminator with temperature-controlled rollers for the lamination and creation of product layers
- Smoothing rollers to level and compact the laminated product film
- Multiple longitudinal cutter for cutting the width of the bars
- Transverse cutter for cutting the length of the bars (also ultrasonic)
- Product cooling tunnel
- Chiller for setting and controlling the temperature in the different areas of the automated system (the temperature can be set from -10°C up to 100°C)
- Centralized electrical panel controlled by PLC with optional remote control and support to control and monitor all the system functions and parameters.
The customer is involved in defining the system layout and various types of components included in order to tailor the machines to the product being produced, while keeping in mind the required production capacity and the available space.
LC240
Lamination width: 240-260 mm
Production capacity: 3,500 - 7,000 bars/h depending on the size and product
System length: from 10 to 18 meters depending on the options installed
LC320
Lamination width: 300-320 mm
Production capacity: 4,500 - 9,000 bars/h depending on the size and product
System length: from 11 to 25 meters depending on the options installed
LC380
Lamination width: 380-400 mm
Production capacity: 6,000 - 12,000 bars/h depending on the size and product
System length: from 11 to 25 meters depending on the options installed
Cleaning the system
Clean the cutting unit with a damp sponge every hour, and with hot water and a sponge or steam at the end of the work shift.
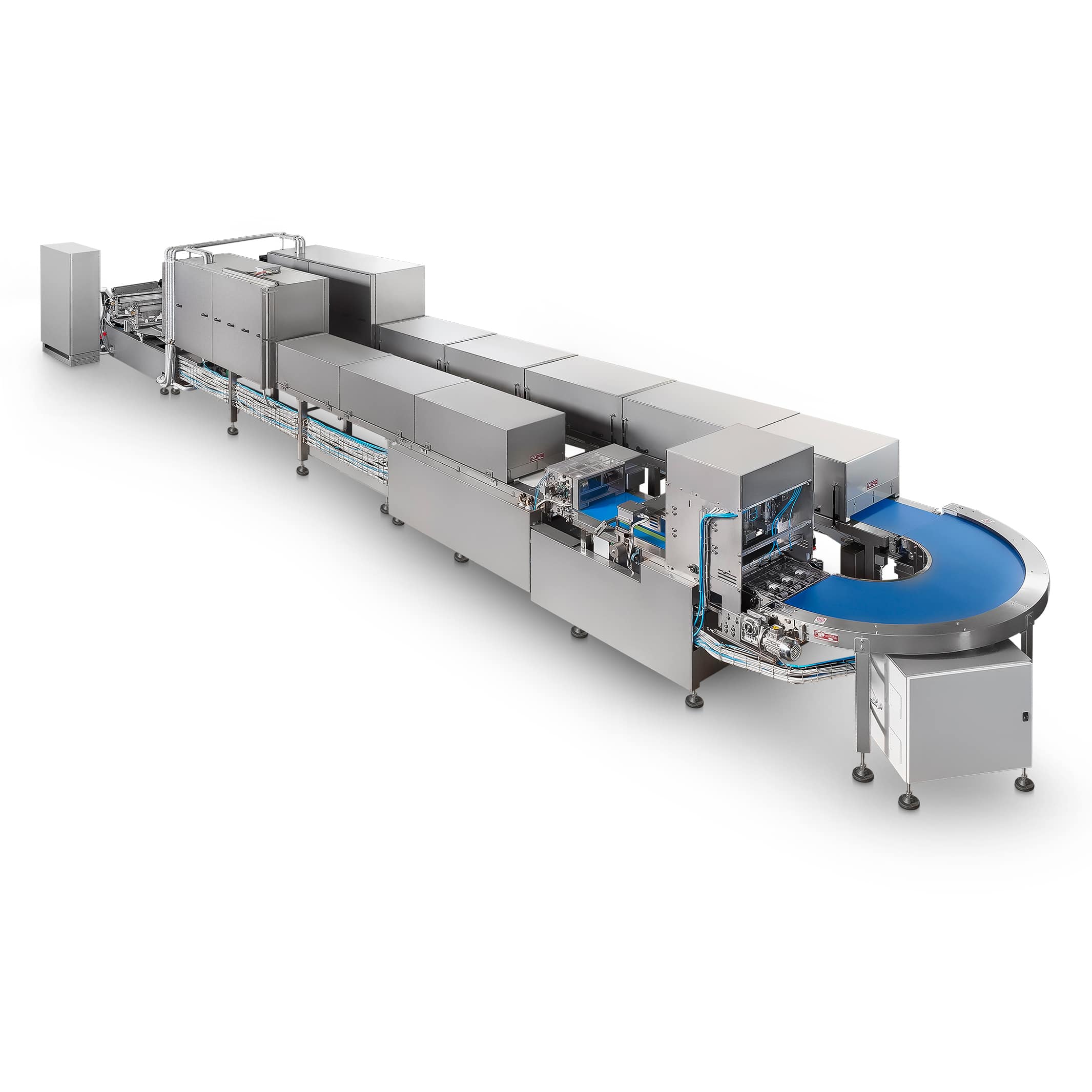
Brittle & Energy bars
Automatic production line
for energy bars and brittle
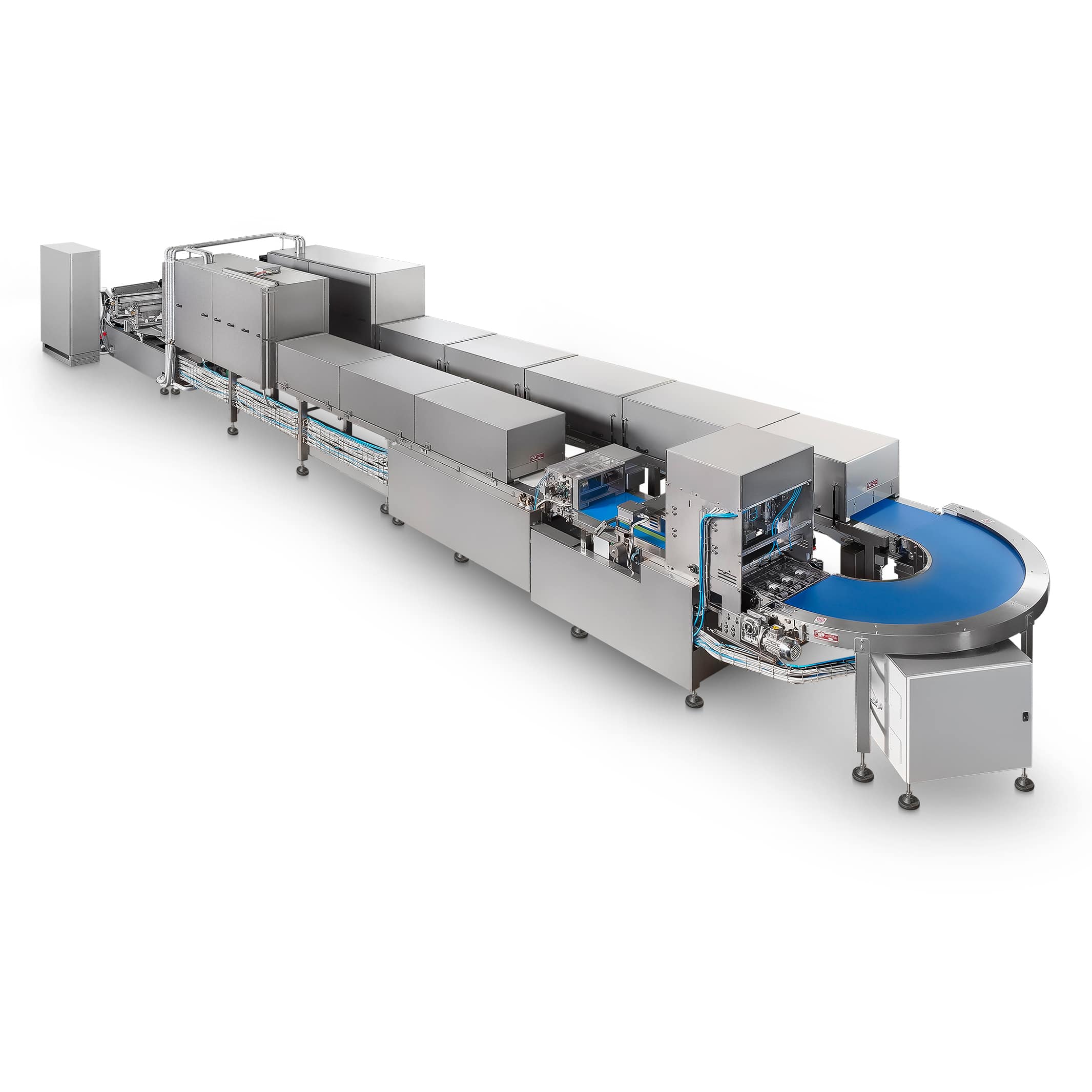
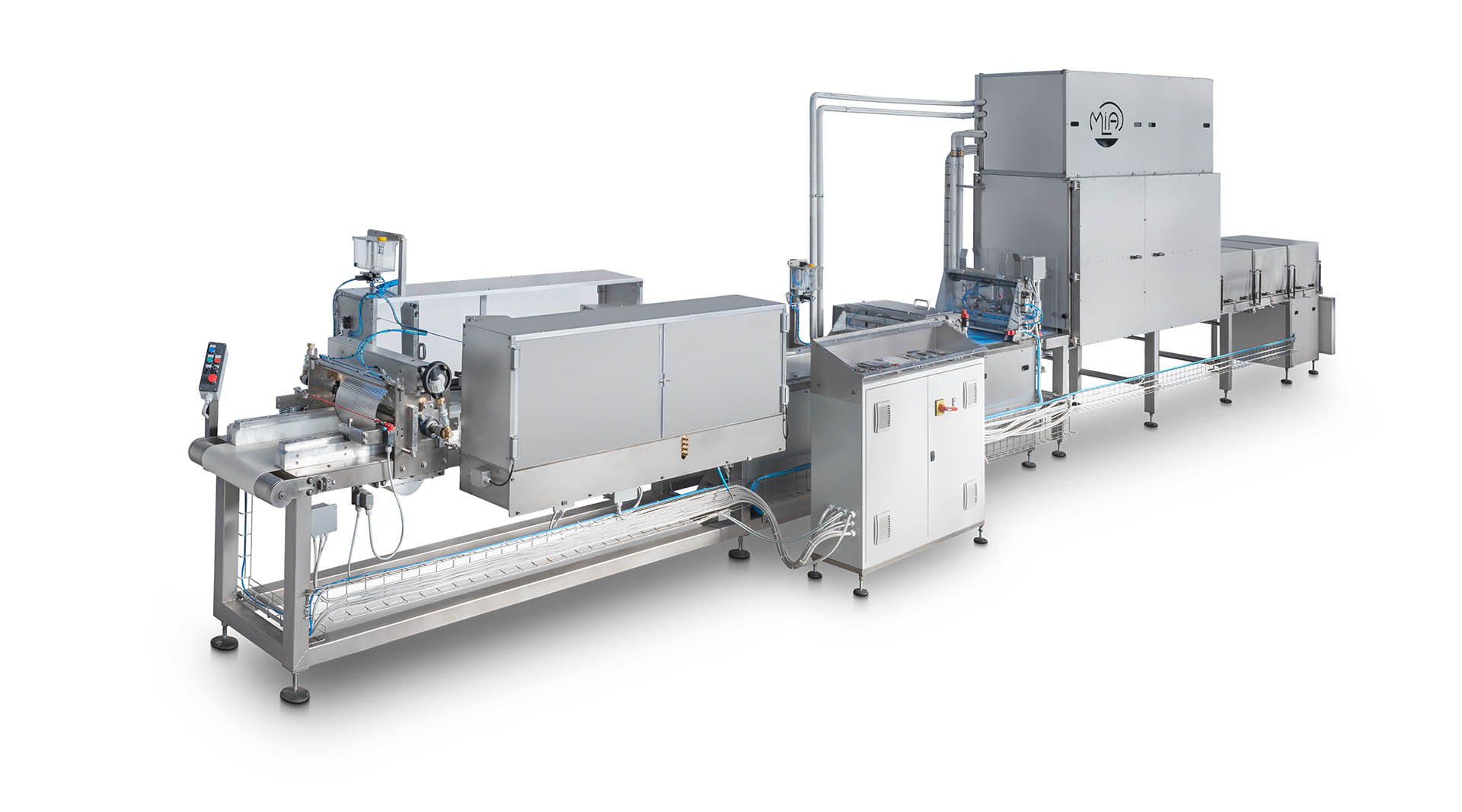
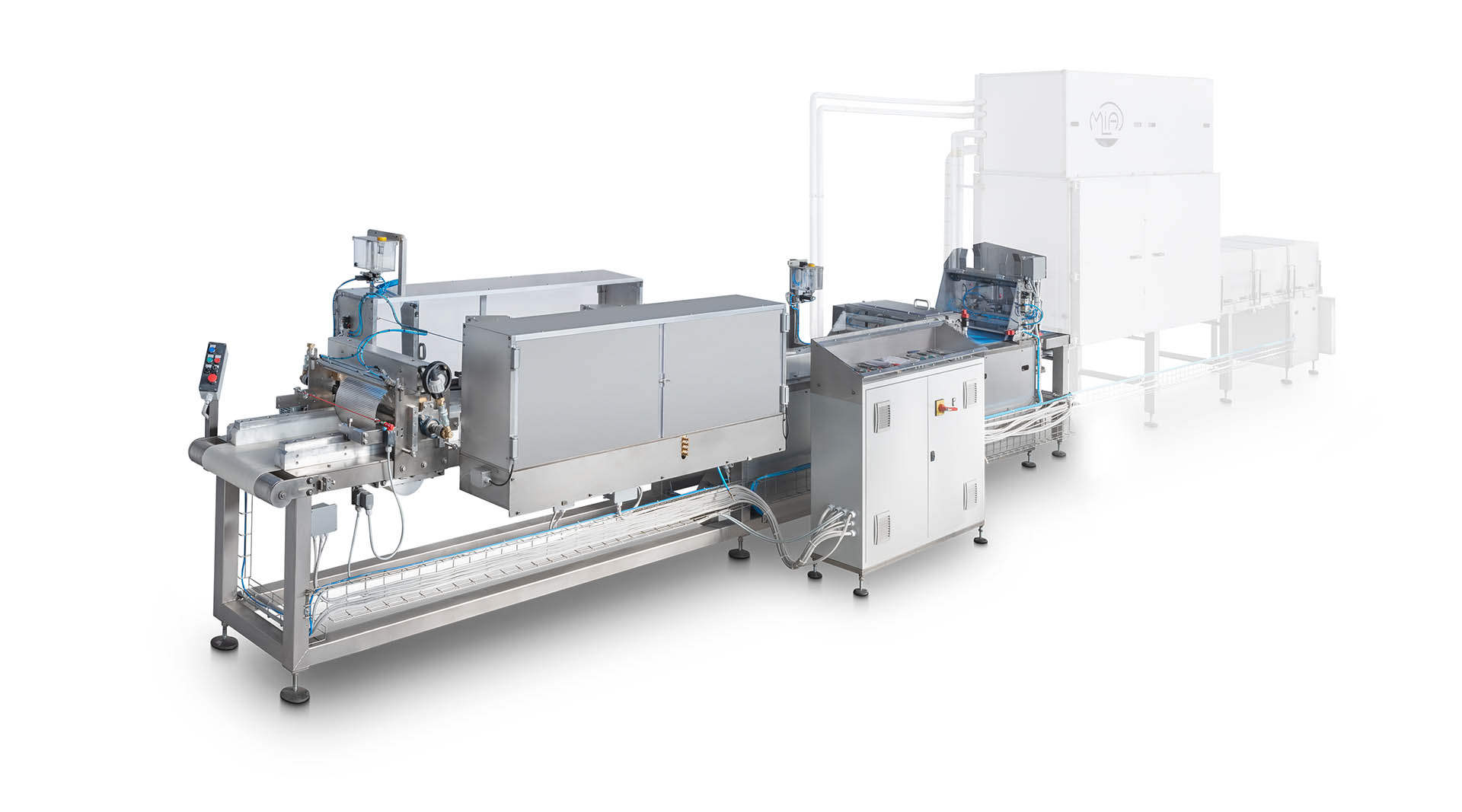