Features
- Machine made entirely of AISI 304 stainless steel
- Robust construction to increase processing precision and long-term durability
- Cutting rollers adjustable up to 20 mm gap
- Cutting roller speed adjustable via inverter
- Production capacity from 150 to 600 kg/h depending on the chopping machine type
- Production: large and small chopped pieces, flour (depending on the machine type)
Technical specifications
- Roller length varies from 200 to 500 mm depending on requirements
- Machine available with 1 to 4 passes
- Optional installation of loading conveyor belt of the product to be processed
- Optional installation of unloading conveyor belt of the processed product
- Optional installation of screen vibrator to sieve chopped pieces and flour
Adjustable cutting system
The cutting system of our chopping machines is designed to adapt to different types of products and obtain excellent precision in the caliber of the chopped pieces.
In the case of nuts, the specific design of the cutting system rollers helps to prevent the extraction of the essential oil from the nuts during the processing stage, thus maintaining the organoleptic qualities of the product and preventing the nuts from rapidly becoming rancid.
System configuration
You can choose CRICK CROCK chopping machines with different configurations from one to four passes to adapt the machine to the customer’s production requirements.
In addition to the number of passes, it is also possible to customize the size of the cutting rollers to have precise and constant control of the size of the product being processed.
Production capacity of chopped pieces
The production capacity of our chopping machines varies from 150 kg/h up to 600 kg/h depending on the size of the machine and type of product to be chopped.
To automate the process and increase the production capacity, our chopping/flour lines can be fitted with loading belts of the product to be processed and unloading belts for the finished products, plus vibrating screens for sorting the caliber of the finished products.
Cleaning the chopping system
Clean the cutting rollers with compressed air as needed, and with hot water and a sponge/steam/compressed air at the end of the work shift.
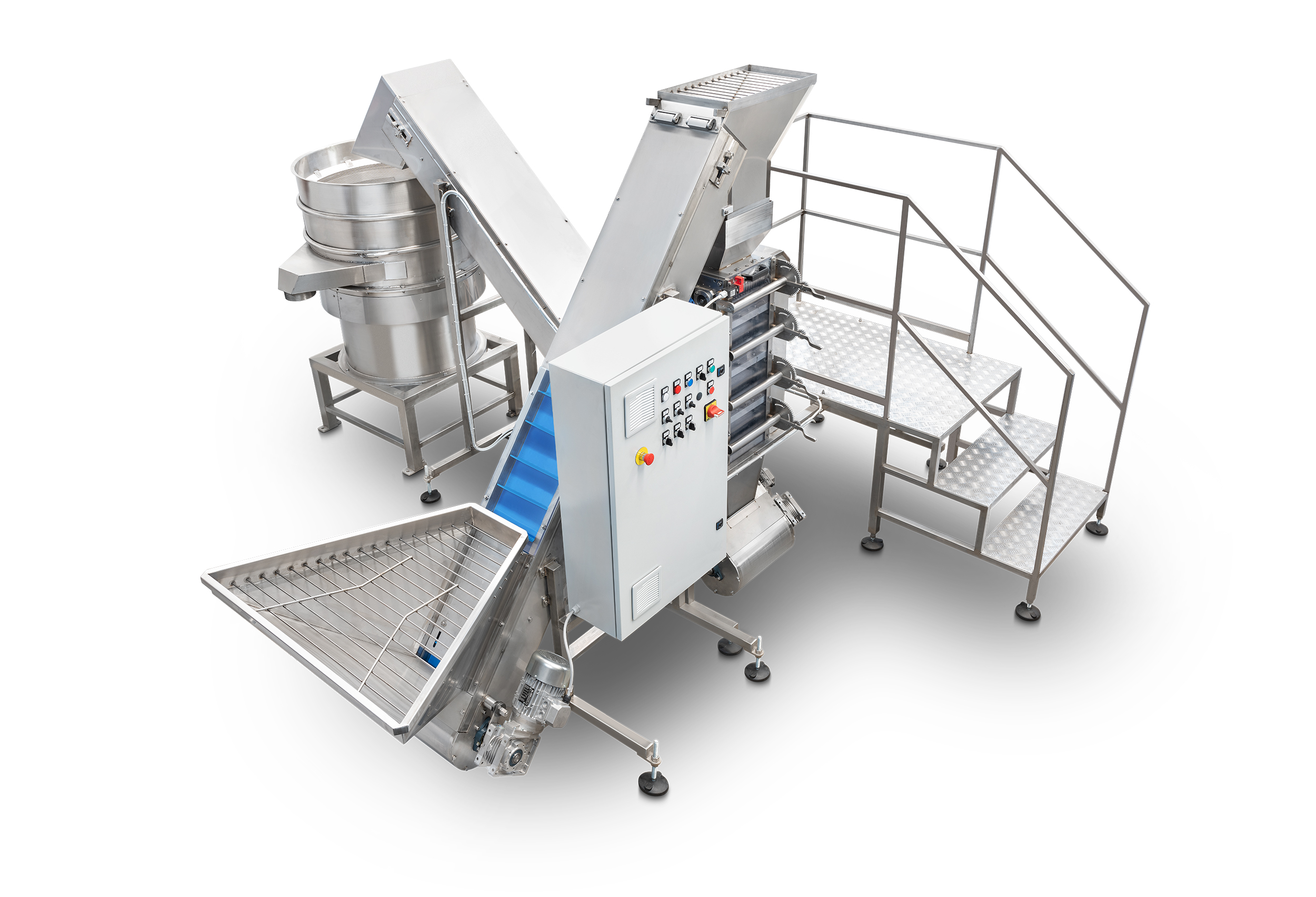
Nuts
Chopped pieces and flour production system
for processing nuts, hazelnuts and seeds